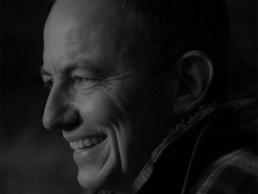
WEEE – A leaky business or key component to circular economy?
Dave Hollingsbee of Stoane Lighting speaks to Nigel Harvey from Recolight, and Stewart Price of Lumicom about the pros and cons of the WEEE Directive.
At the time of writing in the UK there are approximately 115 AATF’s (Approved Authorised Treatment Facilities – companies licenced to carry out teardown, shredding, separation and processing work) and 27 registered PCSs (Producer Compliance Schemes – companies responsible for collection of WEEE on behalf of their producer members). Two of these schemes (Recolight and Lumicom) are the best known in the UK lighting arena, both have contributed to this article.
Since February 2007, the WEEE (Waste from Electrical and Electronic Equipment) Directive has been law in the UK, undergoing substantial changes in 2013. WEEE collection, recycling and recovery targets have been set on an annual basis for household since 2014. For example, in 2022, PCSs were collectively assigned a household WEEE collection target of 4,145 tonnes (lamps) and 5,992 tonnes (luminaires). Those targets were then split among PCSs in accordance with the aggregated market share of their household members.
With improving processing technologies at AATFs, we are seeing impressive recycling and recovery figures. For example, this data shows what materials can be successfully recovered from a batch of waste luminaires:
Recycling is a positive intervention but is not the best solution
Why are we so enthusiastic about remanufacture The data in the above table [fig 1] demonstrates one of the shortcomings of recycling, which is vital to acknowledge if our industry is to fully embrace a circular economy: recycling erodes value. The batch of waste luminaires is converted back into various basic materials – such as metals. Those can be successfully returned into the raw materials supply chain. But all the embedded carbon associated with the manufacture of the original products is lost.
What’s more, a significant proportion – in this case 14.5% – is diverted to “waste to energy”. It is effectively incinerated to produce energy – but in the process, releases carbon. Arguably displacing the equivalent extraction of virgin fossil fuel but nonetheless still contributing to the climate crisis.
The waste hierarchy [fig 2] quite rightly puts recycling below prevention, repair, and reuse. To drive improved sustainability in the lighting sector, we must get much better at applying the waste hierarchy. That means prioritising repair and reuse above recycling. Historically in our industry, we have regarded getting waste recycled as good enough. We need to change that mentality.
So, assuming a fixture has reached a point where re-use, repair or remanufacture are not viable, what does recycling look like?
Significant volumes of higher grade, higher value material are now being responsibly recovered. Dangerous compounds such as the Persistent Organic Pollutants (e.g. brominated flame retardants) and mercury are responsibly separated and kept out of waste streams, water tables etc.
Techniques and hardware are continually improving, similarly the demand for recovered material evolves. Coined in the 1980s the expression “Urban Mining” is now a household term. There is demand for the recovered elements. A recent facility tour of Waste Expert’s Huddersfield facility organised by The Society of Light and Lighting (SLL) offered invaluable first-hand insight to a group of the society members of what the process looks like.
At this stage it has to be noted that research has shown that >165,000 tonnes of household WEEE generated annually never makes it into a registered WEEE treatment facility, and instead is disposed of with general waste. Clearly awareness and infrastructure investment is still needed.
Household and dual use lighting specific figures: the lamps collection rate is quite high – in 2021 around 47% of lamps were collected and recycled. The government is likely to consult on implementing kerbside collection of WEEE for households.
But for non-household fittings, that figure was a lot lower. Only around 6.3% was returned through the PCS network. The fate of the rest is unclear, but it was probably recycled as scrap metal. That is suboptimal, and may mean that some of the hazardous materials were not properly separated and treated.
What WEEE handling provision did you see on site at your last renovation project?
Going back a stage
That is waste capture. But what about perfectly functional kit that is no longer needed by a client/venue? Over recent years we have seen a proliferation of new approaches: Lighting as a Service (LaaS), Buy-back schemes, third party company and OEM initiated remanufacturing offerings.
To properly understand the realities of what happens to redundant lighting equipment, we must look at the options faced on site. We know just what WEEE is and what it is not. There is an obvious challenge to capture more of the missing waste into the correct WEEE channels, but what about the perfectly good equipment that is removed, surplus to requirement, i.e., not part of a LaaS or buy-back scheme or pre-destined for specific remanufacture and re-deployment? Most people reading this article will have seen examples on site of perfectly viable, valuable equipment, piled onto a pallet, stacked in a heap for WEEE processing or thrown into a general waste skip. An opportunity missed. With all the current effort going in to adapting the lighting industry to the circular economy it is preposterous. Is there a solution? Can we find a sustainable route that diverts valuable equipment from simply being pushed down the WEEE route for material and energy recovery?
It seems that the critical juncture occurs on site where a human technician makes a simple A or B* decision (see fig 3). The moment a fixture is assigned “B” status and a place in a WEEE collection receptacle, its only destination is the shredder.
While recovering materials and not components is the ‘ring’ of last resort (as utility is lost and recovered material can be lower grade than virgin) not to mention the energy involved (collection, cleaning, sorting, shredding, processing, transporting), It still plays a crucial role – it keeps materials in use and reduces waste stream. Recycling materials takes less energy than primary production and consequently less GHG emissions. For example, recycling aluminium requires only 5% of the energy used to create primary aluminium.
Conversations with PCSs suggest that early identification of those projects from which fittings could be reused or remanufactured is vital. Where that happens, and if the contractor is supportive, then providing suitable packaging materials, such as “cardboard bubble wrap” could help preserve the product for reuse. This crucially also requires companies that are willing to receive the product and rework it. Recolight has offered to deliver such product, free of charge, to companies in the UK willing to take responsibility for the product. This requires a new “ecosystem” of remanufacturers, willing to receive, remanufacture, and certify the product. That may also involve harvesting of components or subassemblies that are reusable.
Education and motivators could probably be implemented in order to stimulate the A or B decision process on site. But what next? Where should the pallet of good, protected, used equipment go?
Who is to store it? Where?
Who is to process it? How?
Who is to certify it, package it, warehouse it?
The wheres, hows and whos are answerable, but only once the “WHY?” is established.
Fundamentally we require specifiers and end-users to be willing to purchase reused product. That is what will drive this change – the pull of customers willing to purchase reused product. That requires confidence and trust in the remanufacturing process, and the development of the reuse standard BS8887 for the lighting industry should give purchasers the confidence that remanufactured product is fit for purpose. Resetting warranties. The commercials also need to work – it is unlikely that customers will pay more for reused product than they will for new product – Recolight’s offer to deliver reused product FOC should help spark this change.
As David Battersby puts it: There are two points – Education and Price. How does the industry engage with people “on the ground”? Educate and interact, and not just with larger companies, also wholesalers and other stakeholders. Circularity must turn a profit. David believes that while the lighting community may be increasingly aware of circularity, it relies on other parties to make it reality. Interdependency up and down the supply chain. So long as a margin and/or benefit can be identified then there is the “why”.
Answer the “WHY” and WEE PCS’s have the potential to become an even more vital ingredient to the circularity of the lighting industry.
www.greenlight-alliance.com
www.recolight.co.uk
www.lumicom.co.uk
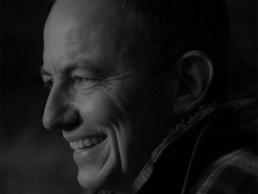