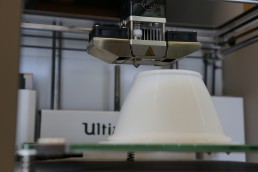
David Morgan Review: LumiAdd
As more companies look to become more carbon neutral, David Morgan examines the luminaire offering from LumiAdd, a new manufacturer that creates 3D printed components for its products.
Luminaire manufacturers are transitioning towards carbon neutrality along several different paths. Some companies extol the use of machined aluminium components produced for each project as the best way to achieve carbon neutrality and comply with a circular economy approach. Others are advocating the use of 3D printed plastic components, and minimising the amount of aluminium employed, as a better approach to achieving similar goals.
It seems be a complex task to determine if either approach will make a measurable reduction in the lighting industry’s contribution to global warming, but a lot of development work is now being undertaken and money spent with the aim of making a difference.
Signify (using its Philips brand) has perhaps made the earliest and largest commitment to the 3D printed approach, and now offers a wide variety of standard and customisable luminaire types produced with recyclable polycarbonate and recycled polycarbonate components. In 2019 it began a roll-out project with Marks & Spencer to produce new luminaires to illuminate their stores all using 3D printed luminaire enclosures, claiming that this would reduce the carbon footprint by up to 47%, excluding the optics and electronics. It is understood that at the end of life, the polycarbonate components will be returned to Philips to be recycled and reused to create new luminaire components.
This approach has now been taken up across the lighting industry and many companies now produce luminaire components using a variety of plastic materials including nylons, polycarbonate, and ABS. Being able to quickly create custom designed components for each project without needing to invest in hard tooling is increasingly attractive as surface quality improves and prices reduce.
At the other end of the corporate spectrum from Philips, a start-up UK company called LumiAdd has just launched an initial range of luminaires using components 3D FDM printed from PLA (polylactic) resin, a biodegradable plastic derived from renewable sources including corn starch, sugarcane, or cassava. In addition to marketing complete luminaires, Lumiadd is supplying PLA components to other lighting companies.
LumiAdd was founded by lighting designer Jamie Norris Green and lighting product designer Lewis Smith in 2022. Jamie is an experienced lighting designer who worked at Aecom and Lumineer before starting his own consultancy in 2013. He has been experimenting with the use of 3D printing for more than 10 years, before starting LumiAdd. Lewis started his luminaire design career at Martech and Cooper Lighting before forming his consultancy in 2015.
The initial LumiAdd range is targeted at the international lighting specification market that Jamie and Lewis are already familiar with, and includes recessed and surface mounted downlights and an adjustable spotlight. One of the great benefits of the 3D printing process is that it allows all orders of the LumiAdd range to be customised with short lead times to meet project requirements, even for small order quantities. The downside with 3D printing is that, to scale up as order quantities grow, the number of printers used will need to increase at more or less the same rate. At some point it may well be appropriate to injection mould some higher volume components, and this can still be done using PLA resins, so the niche that LumiAdd has established can scale to a larger size if demand grows.
The LumiAdd range is constructed using FDM-printed PLA components combined with other parts such as extruded aluminium heat sinks, 90 CRI COB LED light sources and industry standard optics that cannot be 3D printed.
The PLA resin material that Lumiadd uses for its FDM 3D printed parts is sourced from Thailand and is derived from sugar cane. According to a detailed lifecycle impact assessment undertaken by the manufacturer of the resin, Total Corbion, the production of PLA from sugar cane in the tropics is an environmentally sustainable process with a low carbon footprint. They predict that, although at the moment the resins are not currently carbon neutral, with further development and investment they may become carbon negative.
The primary benefit of using bio-plastics, such as PLA, for luminaire components is to minimise their carbon footprint. However, determining the precise reduction compared to using plastics based on petrochemicals seems to be a complicated process and depends on how the components are disposed of at the end of life, as well as the sustainability of the sourcing, manufacturing, and logistics. If they are composted, which can take years under some conditions, then the CO2 that was captured while the sugar cane was growing is released, giving no overall carbon reduction. If the components are reground and reused to make new components, then the original captured carbon is retained but this process uses energy that will have a carbon footprint. Reusing existing printed components disassembled from old luminaires within a circular economy model would ensure that the carbon remains captive, but I predict that the 3D printing process is going to develop rapidly over the next 10 to 20 years with improved quality and lower costs, which may make the reuse of old parts less likely.
The samples that I was sent to review are neatly designed and although the tell-tale surface witness lines resulting from the current FDM 3D printing process were clearly visible, the overall appearance was attractive and when mounted on the ceiling it would not be obvious that these luminaires were not made by conventional processes or materials. The 3D printed springs worked well to hold the downlights into the ceiling with a positive pressure. The surface mounted downlight incorporated a neat 3D printed threaded fixing to a separate mounting plate to eliminate any visible fixing screws. The Bridgelux COB LED light engine and the Ledil lenses were of high quality and the lit effect from the range was good.
The adjustable spotlight incorporated a Ledil zoom lens, which was held into the body with a neat, printed snap fit detail. The design of this product was not as successful of that of the other LumiAdd luminaires in the range. The PLA material is flexible so while handling the body it felt rather insubstantial and the mounting arm was rather spindly. The pin type aluminium heat sink enclosed in the body becomes warm when fully saturated and this seemed to make the body slightly more flexible than when at ambient temperature. When installed on the ceiling these details would not be of great significance but, at the point of sale, I can imagine there might some specifier and customer resistance to the use of PLA material.
LumiAdd has entered the market at a point when specifiers and end users are looking for ways to reduce the carbon footprint of luminaires, so its timing is good. Using 3D printing has many benefits to the lighting industry for low volume customised parts as can be seen by the increasing use of the process, but currently the higher unit costs compared to injection moulded components, whatever the resin type used, is probably going to be an issue with end users.
Using PLA and other bio derived resins for luminaire components seems likely to grow over the coming decades as their production becomes more efficient, and so LumiAdd may have an early adopter advantage in this market niche for the moment. It will be interesting to see how the range and process develops over the next couple of years and to see the type of projects where these luminaires are used.
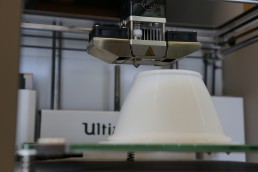